Project Subtitle:
Project Description:
When the Hevenor family approached Steve DeMetrick of DeMetrick Housewrights about building their new home in Wakefield, Rhode Island, they already knew that they wanted a Passive House. This young family of four had purchased an infill lot close to the bike path, easily walkable to the grocery store and the local elementary school. They were looking to build an affordable new home, and liked the predictability that comes with building a Passive House—in many ways eliminating many of the big decisions that come with designing and building any new home.
Steve DeMetrick and architect Steve Baczek worked with the clients to design and build a simple three-bedroom, two-bath home which was builder- and supplier-friendly, using conventional and easily-available building materials. The builder-architect team worked closely with the clients from the beginning as an integrated team, and everyone on the project was committed to the goals of affordability and replicability.
The building features Schuco triple-paned windows and a finished concrete floor (beneath which lies six inches of foam with an insulating R-value of 26). Double-stud walls provide room for 12 inches of thermal insulation (totaling R-55). Blown-in cellulose insulation in the roof is calculated at R-92. By keeping the building’s shape simple, the team was able to complete the project for a total construction cost of $300,420, or $163.00 a square foot. As the first PHIUS-certified Passive House in Rhode Island, this project sets the standard for helping to bring Passive House into the mainstream.
Building Type Summary:
Address:
Elevation:
Lat. / Long.:
Location Type:
Köppen Climate Type:
Climate Region:
Solar Insolation:
Annual HDD :
Annual CDD:
Occupancy Type and Details:
Owner-occupied by family with 2 adults and 2 children.
Conditioned Floor Area:
Conditioned Building Volume:
Multiple buildings?:
Total number of units in project (all buildings):
Total floor area of project (all buildings):
Historic?:
Completion date:
Site description:
Infill lot in a residential neighborhood.
Materials:
One of the main goals of this project was to use locally available materials (local meaning easily sourced from the lumberyard vs. harvested on site) and to keep the construction details builder-friendly. This initial goal was further enhanced by the need to meet a very specific and tight budget. The building shell - framing, insulation - was 100% standard construction. Air sealing was mostly standard with the majority of it coming from zip sheathing and zip tape, and the additional cost coming from the extra caulking we installed at critical joints. The exterior siding costs were kept in check by using #2 eastern white pine (sourced from NH) as the main siding. It was refinished off site and installed as an open rain screen. Both material choice and installation technique led to a very cost effective siding installation. The use of sustainable materials we never a major priority with this project. We did avoid grossly unsustainable products like cellular PVC. The "sustainable" angle we did focus on was in making this construction details we used a affordable and repeatable as possible with the long term goal of inspiring more people to build homes to this higher standard.
HERS Index:
Annual renewable energy generated:
Electric Utility Company:
Datasets and Utility Bills sources and reliability:
From customer's electric bills.
Electricity amount (imported from grid):
Net electricity usage (purchased electricity):
Natural gas amount (purchased energy):
Subslab assembly:
Exposed concrete slab with 6" EPS.
Above grade wall assembly:
Double Stud wall. 2x6 outer, 3" gap, 2x4 inner. 4" closed cell foam Lapolla Foam Lok 2000-4g, 8" blown in fiberglass.
Space heating - Manufacturer & Model:
Space cooling - Manufacturer & Model:
Domestic hot water - Manufacturer & Model:
Domestic hot water - capacity:
Ventilation - Manufacturer & Model:
Process:
We had the unique experience of the customer hiring the builder before the architect. I, as the builder, had the unique opportunity to help the homeowner hire an architect. This approach helped solidify a team committed from the start to design and build to the tight budget we were given.
Design for Adaptability:
Throughout the project, we focused on using construction materials and techniques that were builder friendly with off the shelf materials from the local lumberyard. The only materials not sourced locally were the windows, some of the window tapes, and the Zehnder ERV.
Energy Modeling Software:
PHPP 2007.
Finances Description:
By keeping the building’s shape simple, the team was able to complete the project for a total construction cost of $300,420, or $163.00 a square foot.
Construction hard cost:
Utility incentives:
$4000 for Energy Star Tier 3
$750 for heat pump hot water heater
$300 for minisplit heat pump
Advice:
Steve DeMetrick and architect Steve Baczek worked with the clients to design and build a home which was builder- and supplier-friendly, using conventional and easily-available building materials. The builder-architect team worked closely with the clients from the beginning as an integrated team, and everyone on the project was committed to the goals of affordability and replicability.
Published References:
"The Big Green Fortress", Independent RI: May 1, 2015
http://www.independentri.com/south_county_life/article_e8ddce43-a5b6-55b...
Energy Strategies:
Robust thermal envelope and simple shape.
Energy Use and Production Documentation:
Subslab R-value:
Slab edge R-value:
Above grade wall R-value:
Average window U-factor:
Solar Heat Gain Coefficient:
Cost per square foot of Conditioned Space:
Air Changes per hour, ACH50:
Project Photos:
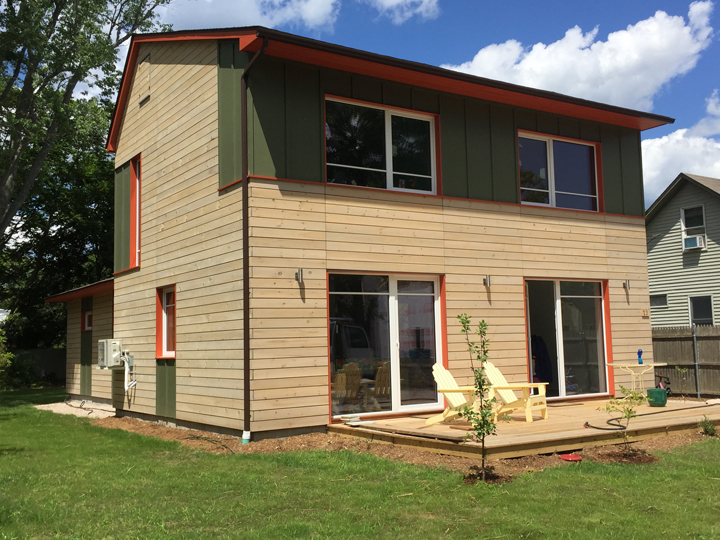
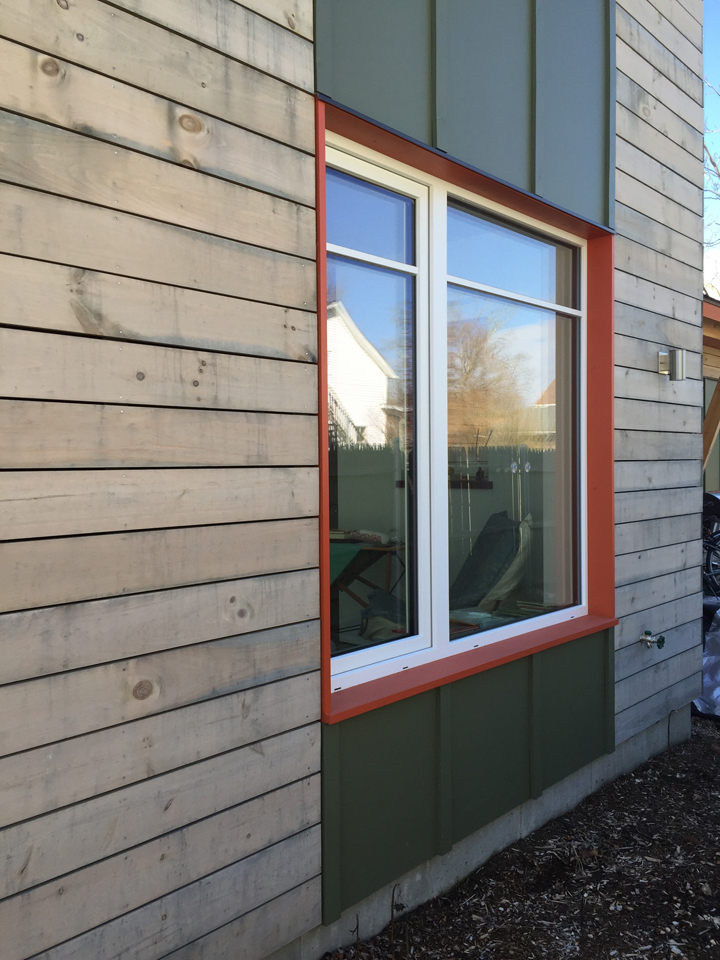
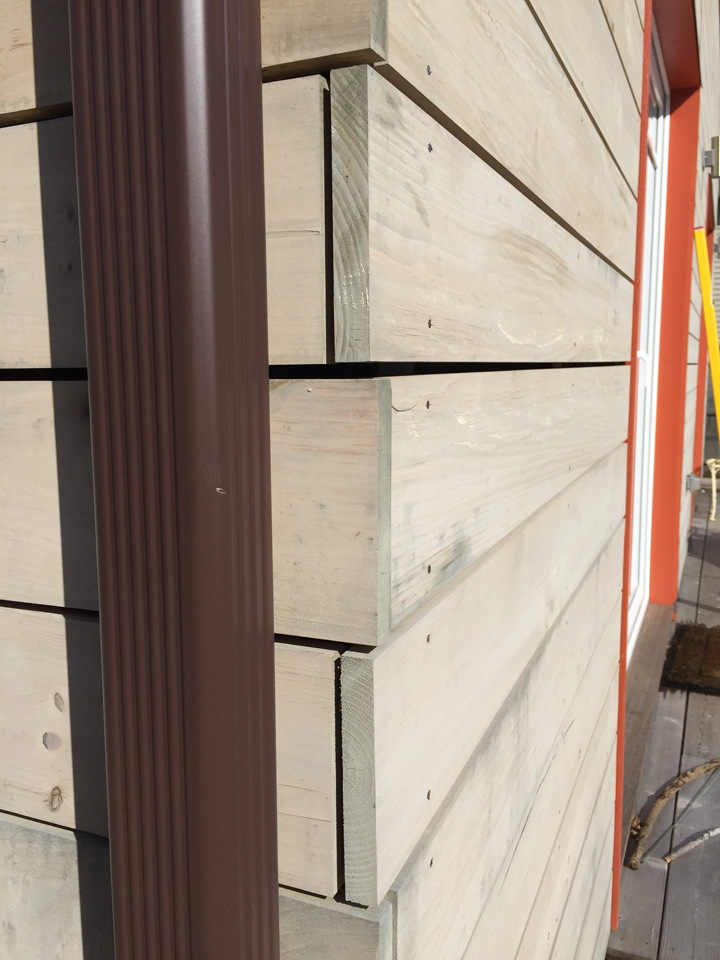
Number of Bathrooms:
Scope Description:
3 bedroom, 2.5 bath single family new construction.
Site conditions:
Other Purchased Fuels Description:
None
Summary of enclosure strategy/description:
This project was designed to meet the PHIUS+ standards, with a robust thermal envelope and simple shape for affordability and constructability.
Roof Assembly:
Truss filled with 24" blown in cellulose.
Roof R-value:
Window Description:
Schuco PVCU, Triple glazed
Door Description:
Schuco
Number of Bedrooms:
Project Team:
Team Member:
Team Member:
Team Member:
Team Members:
Steve Baczek, Architect