Project Subtitle:
Project Description:
DESCRIPTION OF PROJECT:
One barrier to broader adoption of ZNE practice is the perception of ZNE as expensive and exotic. In this project we addressed this issue directly, demonstrating that ZNE renovation can be straightforward and practicable, providing qualitative improvements, significant savings in energy and carbon emissions, and excellent return on investment. We started with our small, simple, relatively efficient, sun-tempered home, our half of a cohousing duplex built in 1994. What would it take to make it ZNE? Answer: Much less than I had anticipated – and nothing fancy.
Our home was built “Energy Crafted”, with 7” dense-packed cellulose walls and tight construction. Our windows were reasonably good for the time – double-pane, argon-filled, low-e casements. A sealed-combustion propane-fired boiler provided heat and hot water. An exhaust-only ventilation system kept the air fresh. Most of the lighting was CFL. The design was compact and sunny, providing a comfortable living space with three bedrooms in about 1,000 square feet of finished area (1,596 SF conditioned space.) A solar hot water system, installed on our roof in 1999, was shared with our duplex-mates. Before our ZNE renovation, our electricity use averaged 300 kwh/month; yearly propane usage was about 300 gallons. A good starting point, but nothing spectacular.
The first step on our ZNE journey followed one of my favorite sustainable design maxims, “Don’t overlook the mundane”: we bought a new refrigerator, saving an estimated 40 kwh per month. Our path to a ZNE home included:
· Careful modeling to determine strategies
· Targeted air sealing (start with a sound envelope!)
· Reducing plug loads
· New air-source heat pump to replace propane boiler
· New HRV to replace exhaust-only ventilation
· Super-insulated electric water tank as new backup for solar hot water
· 5.9 kw PV array to cover all energy uses
With PVs now powering all systems – and in spite of a record-breaking winter – our home was net energy producing the first year: 430 kwh net annual production (1.2 kwh/day, 6.5% above load). With all of this in place, our household energy use declined by 23% (using kwh equivalents for the replaced propane).
Building Type Summary:
Address:
Elevation:
Lat. / Long.:
Location Type:
Köppen Climate Type:
Climate Region:
Solar Insolation:
Annual HDD :
Annual CDD:
HDD Base Temp:
CDD Base Temp:
Occupancy Type and Details:
Owner-occupied, 3 full-time occupants, typical residential occupancy.
Conditioned Floor Area:
Conditioned Building Volume:
Semiconditioned Floor Area:
Multiple buildings?:
Total number of units in project (all buildings):
Total floor area of project (all buildings):
Historic?:
Completion date:
Site description:
Retrofit of existing duplex unit (one side of duplex only) within 32-unit cohousing community.
Materials:
It was a retrofit, with a minimum of new materials. The original construction in 1994 prioritized for sustainable and healthful materials, systems and design. Retrofit involved air sealing; a new, more efficient refrigerator; installation of HRV to replace exhaust-only ventilation; ASHPs to replace propane boiler; super-insulated water tank to back up existing solar hot water; installation of PV.
LCA Description:
No.
Annual renewable energy generated:
Electric Utility Company:
Datasets and Utility Bills sources and reliability:
Meters on building, reliable.
Electricity amount (imported from grid):
Electricity amount (credited or exported to grid):
Net electricity usage (purchased electricity):
Natural gas amount (purchased energy):
Energy Storage type:
N/A, grid-tied PV
CHP System Description:
N/A
Subslab assembly:
1" XPS
Slab edge assembly:
1" XPS
Foundation wall assembly:
8" poured concrete wall with interior insulation.
Most locations: interior stud wall with 6" fiberglass (R-17)
Tight locations (e.g., stairwell): 2" XPS (R-10)
Note: Foundation R-value noted below is approximate weighted average.
Above grade wall assembly:
7” dense-packed cellulose
2x6 stud wall with 2x3 strapping for thermal break
Flat attic assembly:
N/A, this is a cape
Cathedral ceiling assembly:
Cape ceiling
2x12 with 10" fiberglass (vented)
Door Area:
Space heating - Manufacturer & Model:
Space heating - capacity:
Domestic hot water - Manufacturer & Model:
Domestic hot water - capacity:
Ventilation - Manufacturer & Model:
Process:
Defined goals, had our energy geek model several scenarios, chose a cost-effective approach based on modeling.
Energy Modeling Software:
Excel spreadsheet developed by energy consultant.
Outcome of project goals:
Goal was to make home net zero operational energy, including all on-site needs (heating, ventilation, plug loads, hot water). The first year, we were net energy producing. The next year, slightly energy consuming. On average over the past 5 years, we have been net consumers by 390 kwh, or about 5% of all the energy used by our home. (So on average we are 95% to ZNE.) We have had to replace both ASHPs, due to corrosion of coils likely caused by non-expert installation - we may have suffered inefficiency in the past few years due to ASHP performance degradation. An important lesson learned: Hire a very experienced and thorough ASHP installer!
Another interesting lesson learned: We conducted an initial blower door test with 2 blower doors, one on our unit and one on the other duplex unit. When we did air sealing, one blower door was used to monitor improvement, which appeared to be substantial. Subsequent to that, we had the old heating and ventilation systems removed and the new ASHPs and HRV installed. A subsequent blower door test with 2 blower doors showed greater leakage than before we started the renovation. Likely the mechanical renovation did this, or was there some other explanation? Somehow, we were still ZNE, but maybe we just oversized our PV system. We are overdue for some more investigation of leaks and air sealing (unless it turns out the last test was somehow faulty).
Discrepancies:
No.
Total Cost of Project:
Construction hard cost:
Gross Cost of Renewable Energy System:
Value of Tax Credits for renewable energy systems:
Net Cost of renewable energy systems:
Federal incentives:
PV System:
$14,580 tax credit
State incentives:
PV System:
$10,500 rebate from Massachusetts Clean Energy Center
$1,000 MA tax credit
Utility incentives:
Heat pumps:
$1,000 rebate
Annual Electric Savings:
Annual Revenue from SRECs or other renewable energy credits:
Advice:
Note: The annual electric savings above also include the propane savings from removing the existing boiler.
Reflections: Don't overlook the mundane. A small, simple project can pack a lot of savings.
Published References:
Essay about the ZNE renovation published in Earth Matters book, Levellers Press: https://store.collectivecopies.com/store/show/6
Two essays (including the one above) published in Earth Matters series, Daily Hampshire Gazette, Northampton, MA (http://www.gazettenet.com/)
Special architectural measures:
The existing home was sun-tempered, well-insulated, and reasonably tightly built. The retrofit included targeted air sealing to improve performance. I think we need to go back and verify the air sealing, as I have reason to suspect that the mechanical installation may have resulted in breaches in the air barrier. (In spite of this, the home was net energy producing in the first year.)
Energy Strategies:
5.9 kw PV array installed on south facing roof, grid-tied. There was already an existing solar hot water system on the roof, shared with the other unit of the duplex.
Energy Use and Production Documentation:
Subslab R-value:
Slab edge R-value:
Foundation wall R-value:
Above grade wall R-value:
Cathedral ceiling R-value:
Average window U-factor:
Door U-Factor:
Cost per square foot of Conditioned Space:
Project Photos:
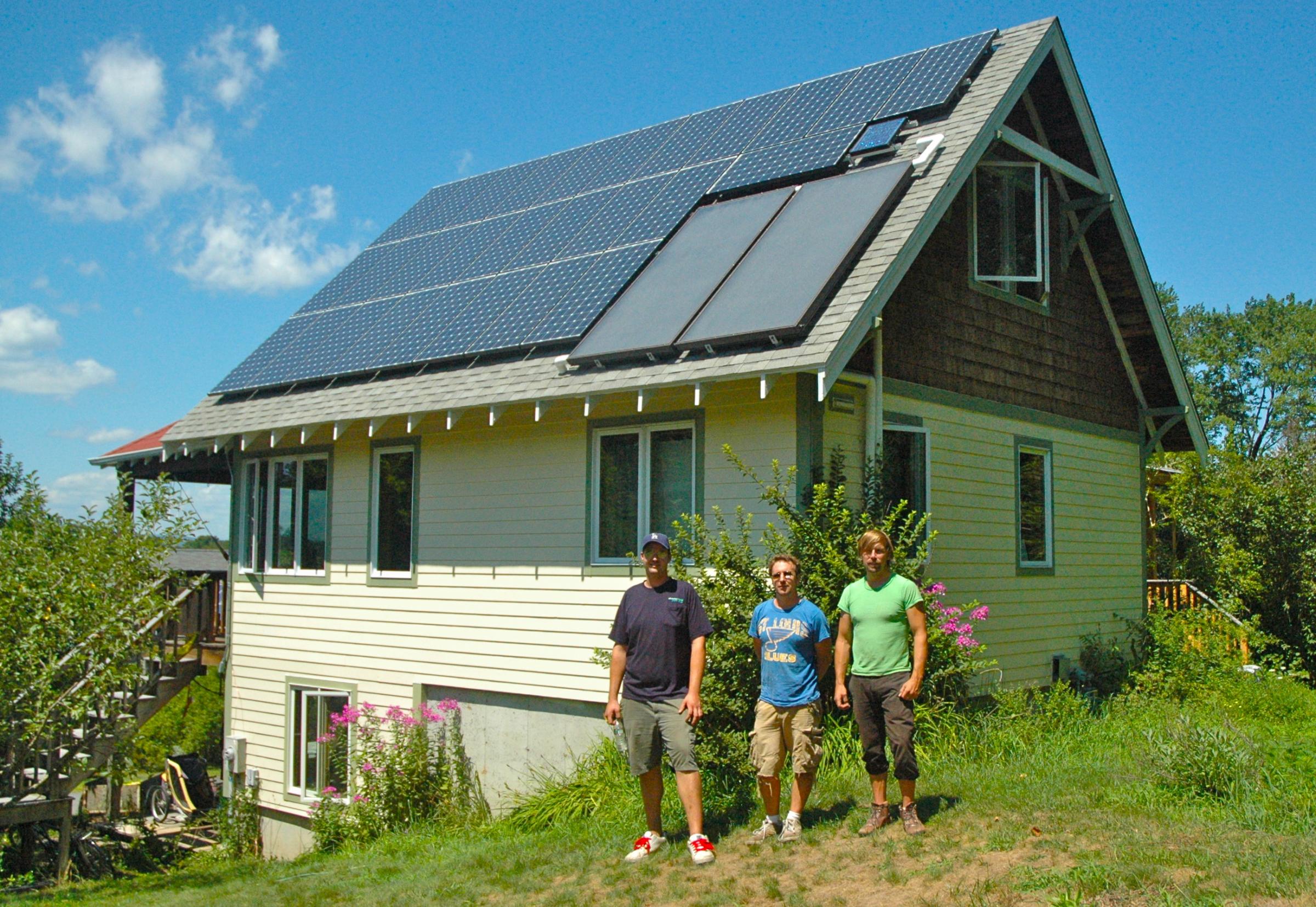

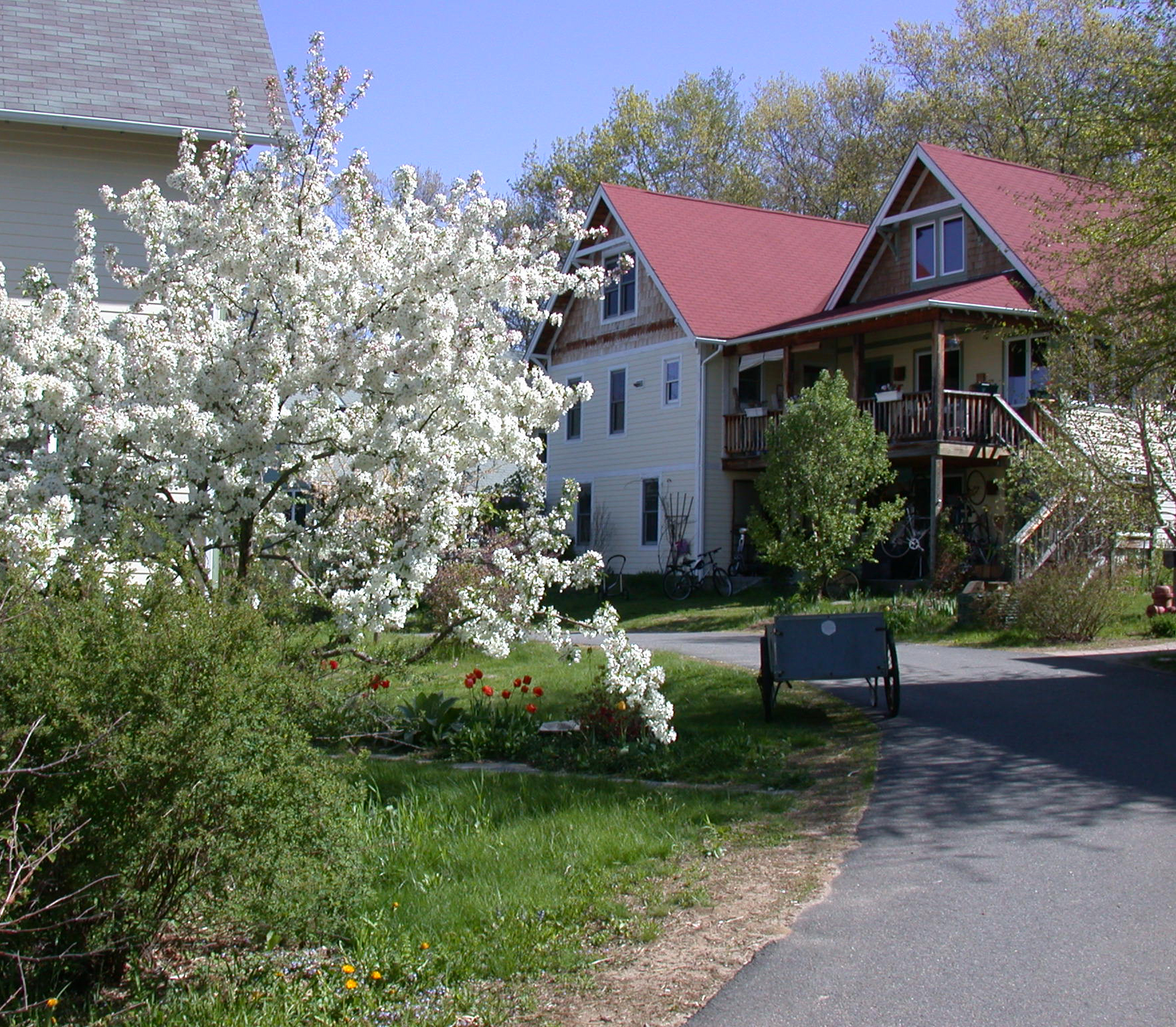
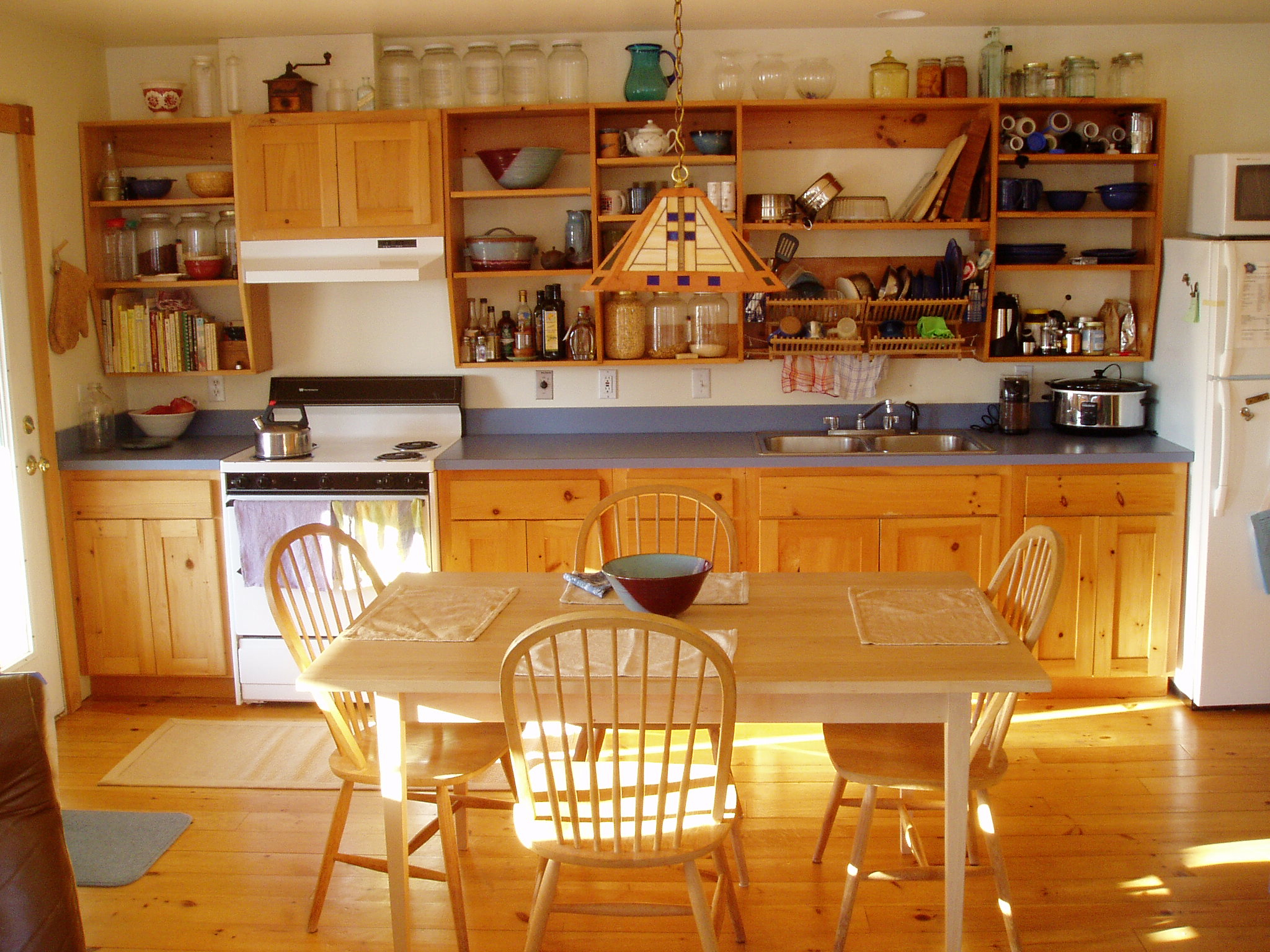
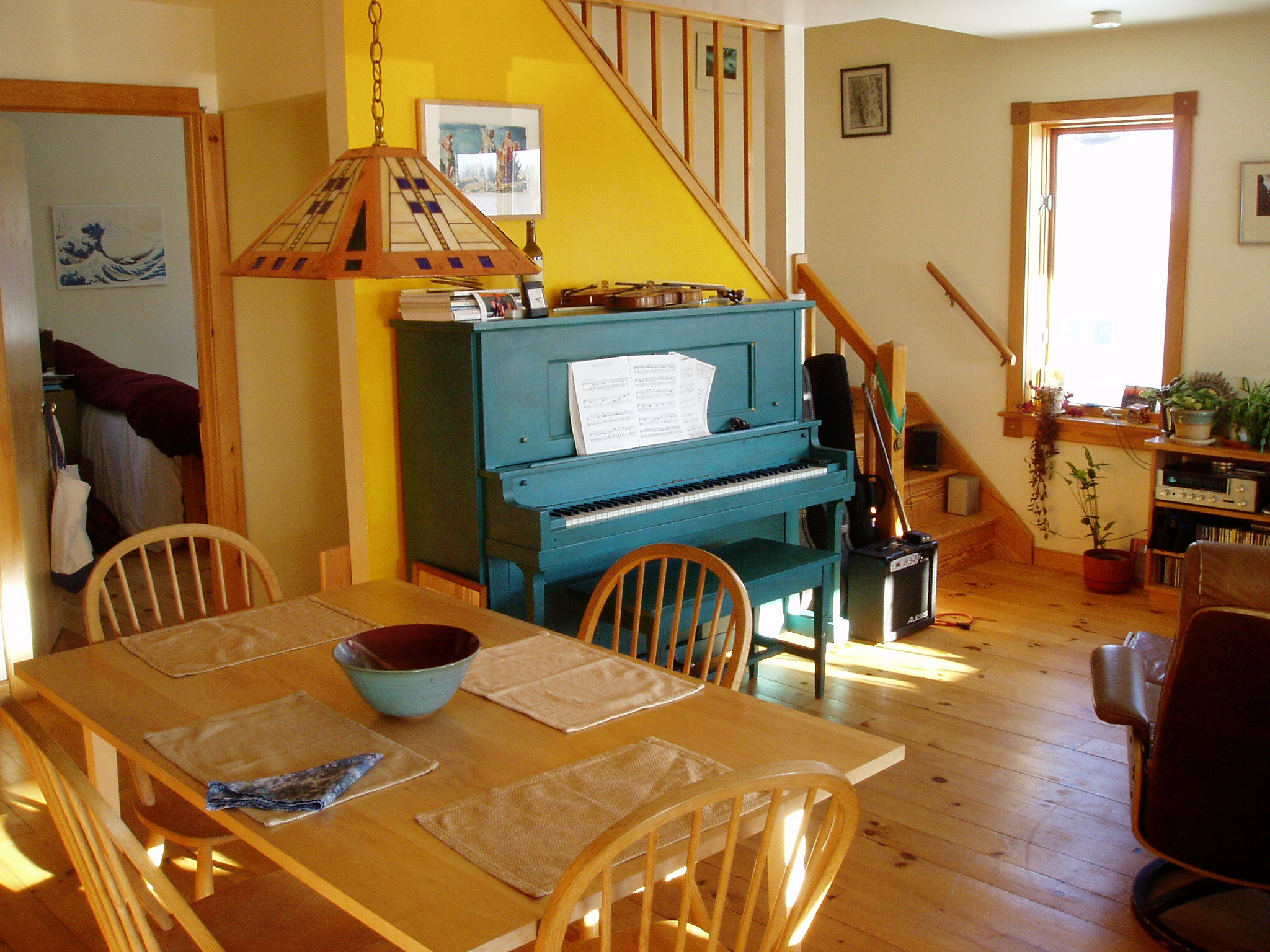
Number of Bathrooms:
Scope Description:
Existing home. Air sealing, reduction of plug loads, replacement of propane-fired heating and hot water with electrical, addition of PV.
Site conditions:
Renewable Energy Sources:
Other Purchased Fuels Description:
No
Summary of enclosure strategy/description:
Targeted air sealing to an already reasonably tight, well-insulated building originally built in 1994.
Roof Assembly:
See cape ceiling above
Window Description:
Existing Weathershield clad wood casements, double-glazed, low-e, Argon-filled.
Do not have information on SHGC and VLT
Door Description:
Existing insulated steel doors (Therma-Tru?)
One with full window, R-3.2
One with half window, R-5
Number of Bedrooms:
Project Team:
Team Member:
Team Member:
Team Members:
Center for Ecological Technology - air sealing
Northeast Solar - PV design & installation, solar hot water renovations
Mechanical Equipment Installation Details and Comments:
Lesson learned: It appears the mechanical work, conducted after air sealing, may have introduced significant air leakage. We have yet to have energy auditors return to find out if this was the case, or whether there is another explanation for the following: An initial a 2-door blower door test (1 door on each unit of the duplex to equalize pressure) showed 503 ACH50 for the unit to be renovated. During air-sealing, a one-door blower door test showed a reduction from 850 to 739 ACH50 for the duplex. As only the one unit was air sealed, one would expect the 111 reduction would apply only to that unit, resulting in 392 ACH50. However, a 2-door test performed after mechanical work showed 640 CFM50. (No sleuthing for location of air leakage was done at the time, for reasons too complicated to explain.) That last number is listed below, even though there is still an element of doubt.